CNC turning is a cornerstone of modern manufacturing, combining automation, precision, and scalability to produce high-quality cylindrical components. From aerospace fasteners to medical implants, the applications of CNC turning span across virtually every industrial sector.
This article explores the core principles, tools, parameters, and real-world applications of CNC turning, enhanced with data tables and clear formatting to help engineers and procurement teams make informed decisions.
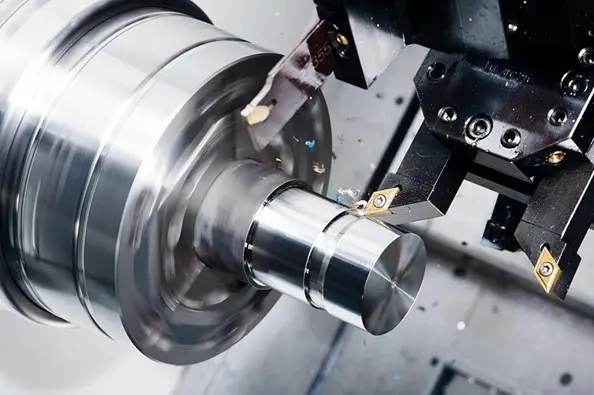
๐ What Is CNC Turning?
CNC turning is a subtractive machining process where a rotating workpiece is shaped by a stationary cutting tool. Controlled by computer programming (G-code), CNC turning delivers exceptional precision for creating symmetrical, cylindrical, and complex geometries.
๐ Unlike CNC milling, in CNC turning the workpiece rotates while the cutting tool stays stationary or moves along defined paths.
๐งฉ Components of a CNC Turning Center
Component | Description |
---|---|
Spindle | Rotates the workpiece at high speed. |
Chuck | Holds and grips the workpiece; may have 3 or 4 jaws. |
Turret | Houses multiple cutting tools, indexed automatically. |
Tool Inserts | Replaceable carbide or ceramic tips for cutting, shaping, or drilling. |
Controller (CNC) | Interprets G-code and controls motion of axes and tools. |
Modern CNC turning centers may include live tooling, bar feeders, and coolant systems, enabling simultaneous turning, drilling, and milling.
โ๏ธ CNC Turning vs. Other Processes
Process | Workpiece Movement | Tool Movement | Best For |
---|---|---|---|
Turning | Rotating | Linear / controlled | Cylindrical, round, symmetric parts |
Milling | Stationary | Rotating + multiple axes | Flat surfaces, complex geometries |
Grinding | Rotating | Abrasive wheel motion | Ultra-fine surface finishes |
Drilling | Stationary/Rotating | Rotary linear | Creating holes along axial path |
Turning excels in speed and precision for parts like rods, shafts, spacers, and bushings.
๐งช Cutting Tool Materials & Coatings
The performance of a CNC turning operation is heavily influenced by the cutting tool material, geometry, and coating. Here’s a simplified comparison:
Tool Material | Suitable For | Hardness (HV) | Heat Resistance | Wear Resistance |
---|---|---|---|---|
Carbide | General purpose metals | ~1800 HV | โ โ โ โโ | โ โ โ โ โ |
Ceramic | Cast iron, hard alloys | ~2200 HV | โ โ โ โ โ | โ โ โ โโ |
CBN | Hardened steels | ~3000 HV | โ โ โ โ โ | โ โ โ โ โ |
Diamond (PCD) | Aluminum, composites | ~7000 HV | โ โ โโโ | โ โ โ โ โ |
๐ก Note: Coatings like TiAlN, AlโOโ, and Inveioยฎ technology improve tool life by reducing heat buildup and improving chip flow.
๐ Typical CNC Turning Parameters
Parameter | Typical Range | Description |
---|---|---|
Cutting Speed | 80โ300 m/min | Depends on material; higher for softer metals |
Feed Rate | 0.05โ0.5 mm/rev | Depth of tool engagement per revolution |
Depth of Cut | 0.1โ5 mm | Material removed per pass |
Tolerance | ยฑ0.01 mm to ยฑ0.002 mm | Depends on machine capability and material stability |
Surface Finish | Ra 0.4โ3.2 ยตm | Achievable via finishing and tool selection |
๐ Types of CNC Turning Operations
Operation | Purpose | Example Use Cases |
---|---|---|
Facing | Create a flat surface perpendicular to the axis | Part end finishing |
Straight Turning | Reduce the diameter along the length | Shafts, rods |
Taper Turning | Produce conical shapes | Pipe fittings, tapered pins |
Grooving | Add recesses or undercuts | O-ring seats, snap ring grooves |
Boring | Enlarge an existing hole | Cylinder bores |
Drilling | Add axial holes to rotating parts | Flange holes, connectors |
Threading | Generate internal or external threads | Screws, bolts, pipe fittings |
Knurling | Impress grip pattern without cutting | Handles, knobs |
๐ญ Real-World Applications
Industry | CNC Turned Components |
---|---|
Aerospace | Fasteners, bushings, landing gear pins |
Automotive | Axles, gear shafts, engine parts |
Medical Devices | Bone screws, surgical rods, orthopedic pins |
Oil & Gas | Couplings, pipe fittings, valve components |
Electronics | Connector pins, sensor housings, antenna bases |
CNC turning is often combined with CNC milling in a hybrid system to handle multi-functional part geometries in a single setup.
โ Key Advantages of CNC Turning
- High Precision: Micron-level tolerances reduce post-processing.
- Repeatability: Perfect for medium to high-volume production runs.
- Speed: Automated processes reduce cycle time significantly.
- Safety: Operators are shielded from direct contact with tools.
- Design Flexibility: Supports rapid design iterations.
๐ง Pro Tips for Better CNC Turning
- Use correct insert geometry for specific materials.
- Balance spindle speed and feed rate to reduce tool wear.
- Optimize chip evacuation using high-pressure coolant systems.
- Choose coated tools for high-temp or abrasive materials.
- Verify G-code in simulation before running production.
๐ Conclusion
CNC turning is not just a machining processโit’s a strategic tool in modern digital manufacturing. With the right equipment, parameters, and material understanding, engineers can achieve highly accurate parts at scale, on time, and with minimal waste.
Whether youโre prototyping a new component or launching mass production, investing in CNC turning technology is a move toward precision, reliability, and competitiveness.
Leave a Reply